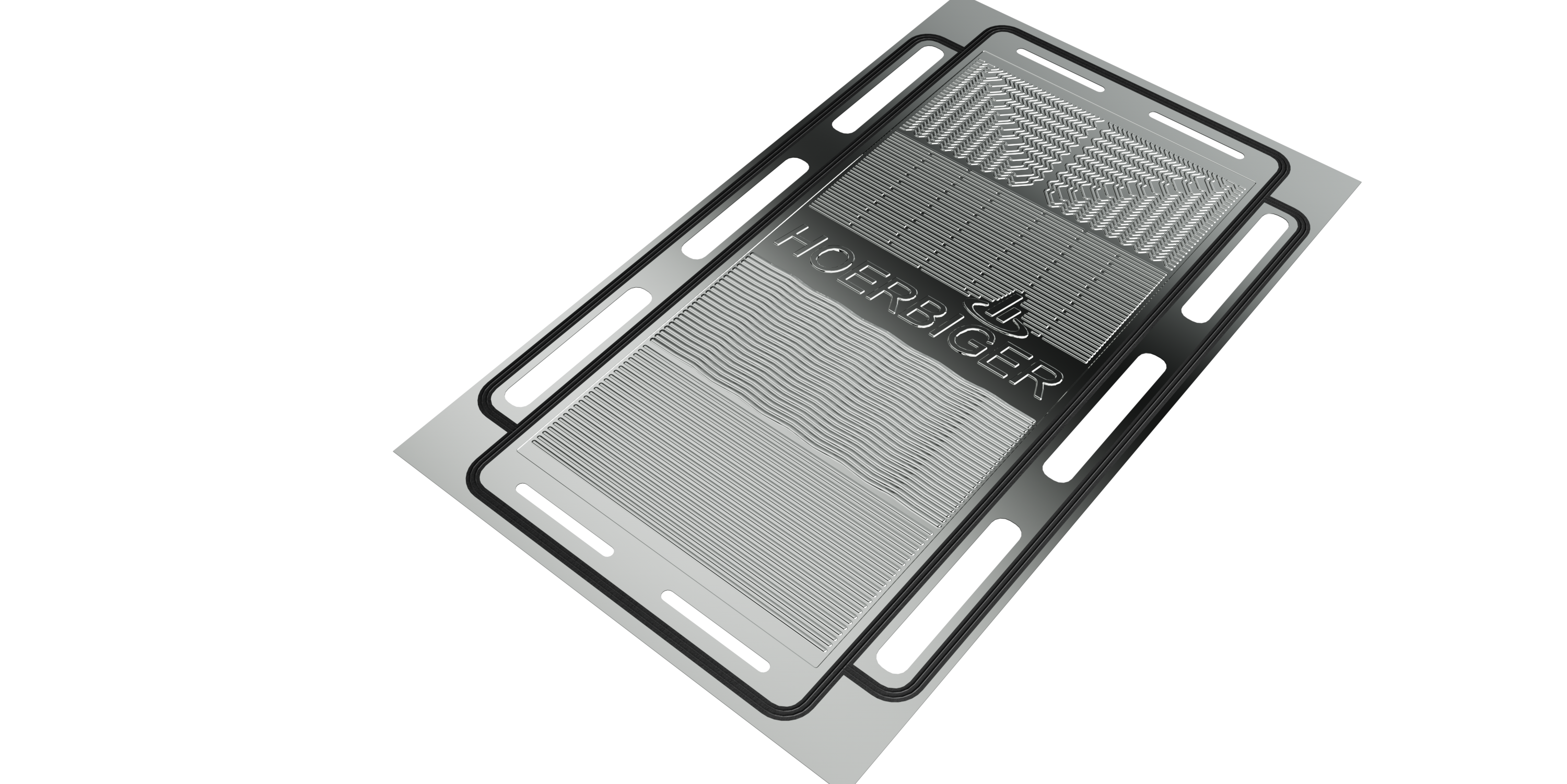
Bipolarplatten und Stack-Komponenten
Enabling Green Hydrogen
Komponenten für Elektrolyseure
HOERBIGER bietet Komplettlösungen für metallische Bipolarplatten und Stack-Komponenten aus einer Hand. Unser Ansatz „simply sorted“ ermöglicht die Entwicklung, Produktion und Validierung der Komponenten unter einem Dach, um ein bestmögliches Produkt zu gewährleisten. HOERBIGER übernimmt sämtliche Fertigungsschritte bis zur fertigen Komponente.
Dank unserer optimierten Prozesstechnologie aus der Automobilindustrie schaffen wir echten Mehrwert für Anbieter von Stack- und Komplettsystemen. Die von HOERBIGER entwickelte Bipolarplatte wird in Zusammenarbeit mit einem technischen Kooperationspartner vermarktet und vertrieben.
Profitieren Sie von unserer Expertise und erleben Sie höchste Effizienz und Qualität für Ihre Anwendung.
Warum wir der richtige Partner für Sie sind
- Frühzeitige Kooperation im Engineering: Bereits in den frühen Designphasen arbeiten wir eng mit Ihnen zusammen, um ein bestmögliches „design to manufacture“ sicherzustellen.
- Optimale Performance und Robustheit: Komplettlösungen zur Steigerung der Effizienz und Stack-Lebensdauer durch verringerte Materialdegradation.
- Perfekte Kompatibilität: Beschichtungen, Substrate und Dichtungen werden sorgfältig mit Qualitätskontrollen abgestimmt, um eine reibungslose Integration zu gewährleisten.
- Ihr Partner für die Industrialisierung: Nahtlose und kosteneffiziente Skalierung mit flexibler Anpassung an die Marktnachfrage.
- Vereinfachte Lieferkette: Durch die Konsolidierung von Prozessen reduzieren wir den logistischen Aufwand für unsere Kunden um 80 Prozent.
- Über 40 Jahre Automobil-Erfahrung: Wir streben 100-prozentige Lieferperformance bei null Fehlerquote (0 ppm) an. Unsere Zertifizierungen finden Sie hier.
Bedarfsanalyse und Machbarkeitsstudie
HOERBIGER bewertet die Kundenanforderungen, um einen optimalen Prozessfluss zu definieren. Dazu werden gängige Methoden wie z. B. CFD-/FEM- und Umformsimulationen angewendet. Ebenso können dadurch Partner und Lieferanten bestmöglich ausgewählt werden.
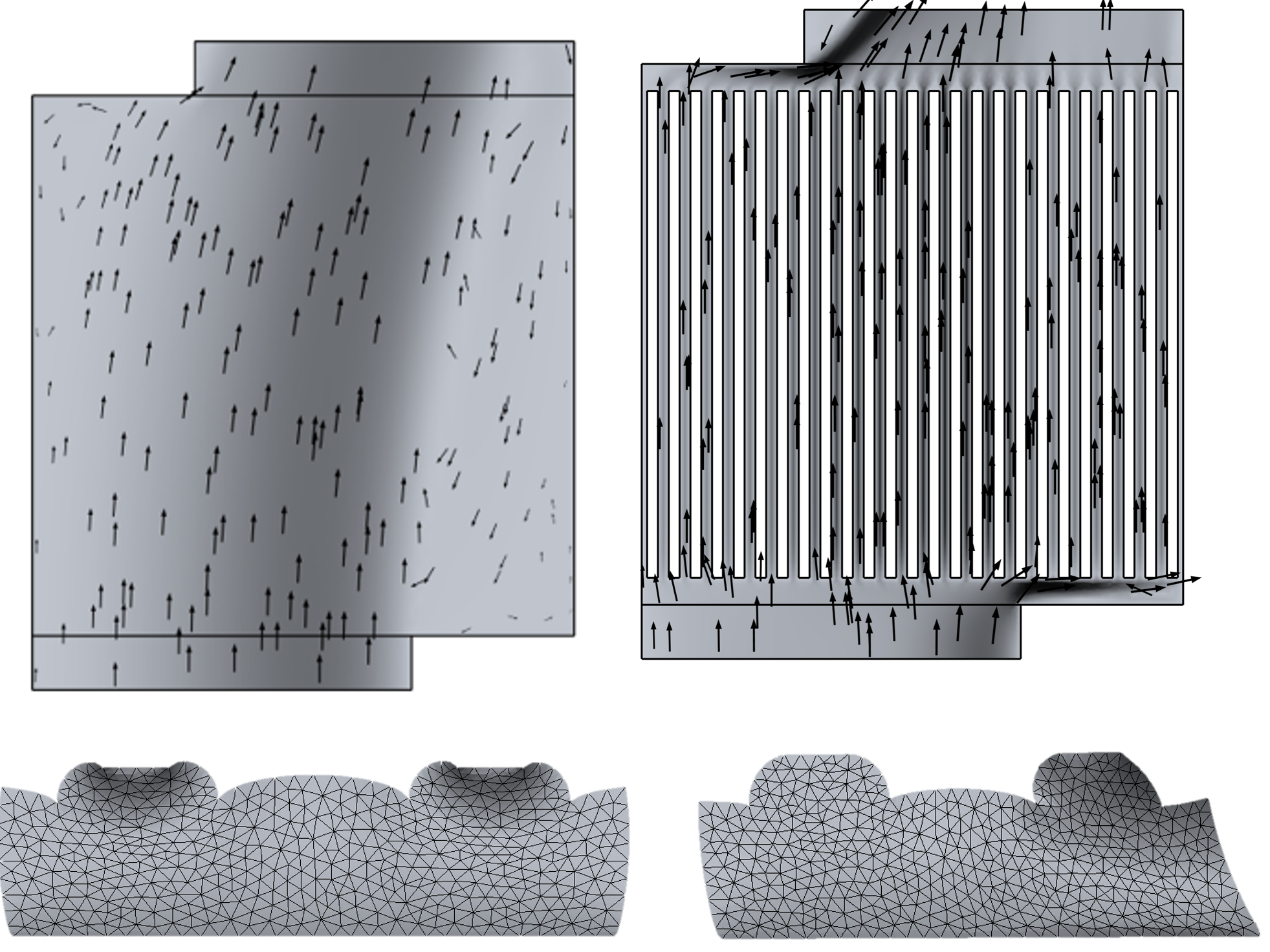
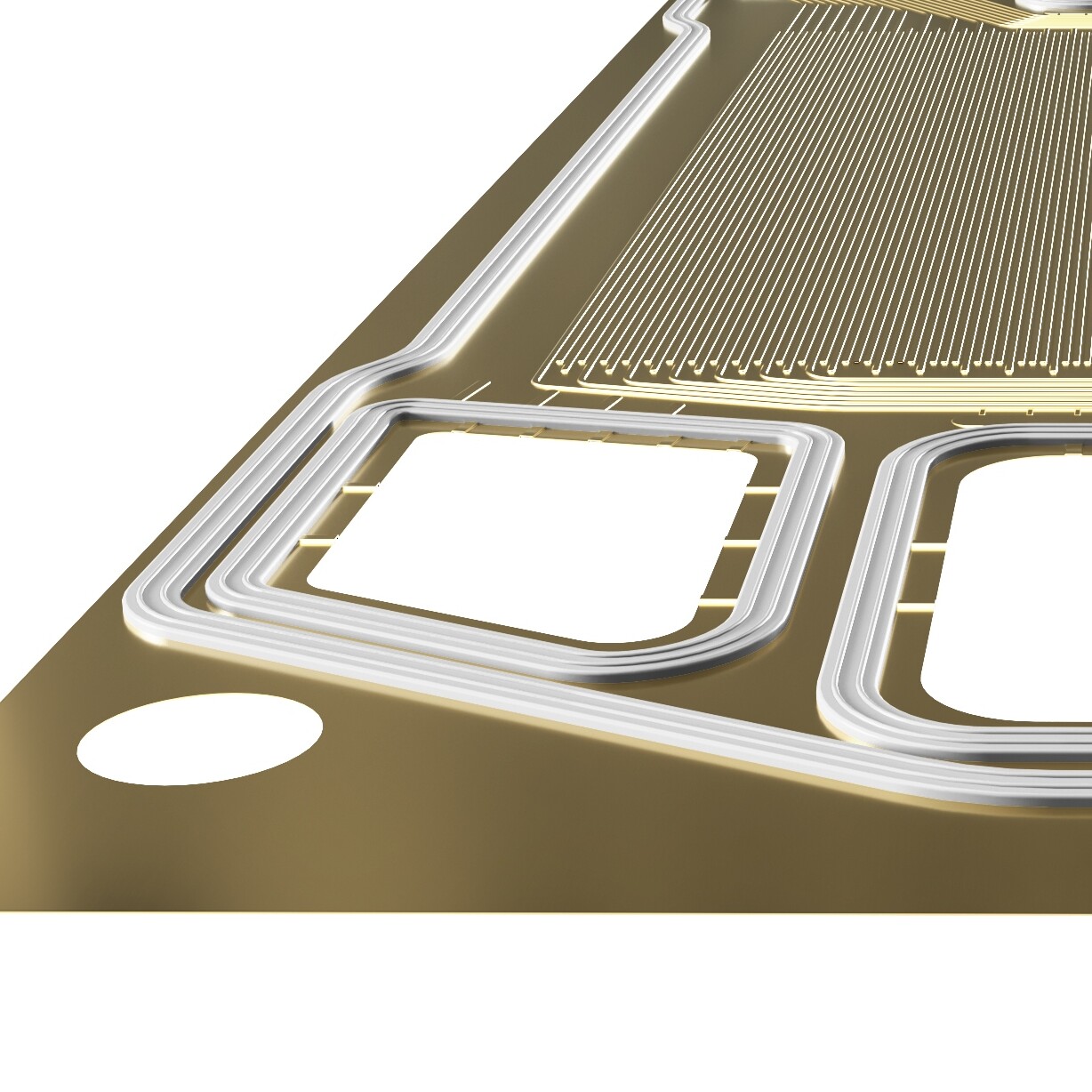
Entwicklung eines robusten Bauteildesigns, Materialauswahl und Spezifikation
HOERBIGER optimiert das Bauteildesign zusammen mit dem Kunden. Wir sehen uns in einer beratenden Rolle hinsichtlich der Prozesskette, um die Komponenten nicht nur funktional, sondern auch prozesstechnisch weiterzuentwickeln. Dies senkt Kosten, erhöht aber auch die Robustheit und Qualität der Bauteile.
HOERBIGER nutzt eigens spezifiziertes Material (beispielsweise für Titan), welches konkret auf die Bedürfnisse der Blechumformung angepasst ist. Dadurch ist eine noch präzisere Umformung möglich und die Bauteilqualität wird weiter stabilisiert.
Blechumformung, Stanzen und Laserschweißen
Die Blechumformung stellt eine Kernkompetenz der HOERBIGER Division Automotive dar. Jahrzehntelange Erfahrung von blechumgeformten Getriebe-Komponenten für die globale Automobilindustrie bilden die Basis für höchste Qualität bei mittelgroßen bis sehr hohen Volumina der Bauteile. Die interne Entwicklung und Fertigung der benötigten Werkzeuge und Vorrichtungen garantieren Innovation und Flexibilität für höchste Kundenansprüche.
Dieses Know-how übertragen wir auf die Herstellung von metallischen Bipolarplatten, gefertigt aus Titan und Edelstahl mit Blechstärken zwischen 0,1 bis 1 mm und mit aktiven Bereichen von 3.000 cm2 und mehr.
Das Verschweißen im Bereich der Bipolarplatten ist abhängig vom Konzept des Kunden. Bei Bedarf verschweißt HOERBIGER verschiedene Komponenten aus Blech auf modernen Laserschweißanlagen. Mustermengen können bereits in-house produziert werden, die Skalierung ist ebenso möglich. Die Erfahrung im Werkzeugbau hilft hier beim Vorrichtungsbau, um insbesondere die hohen Anforderungen an die Dichtheit sicherzustellen.
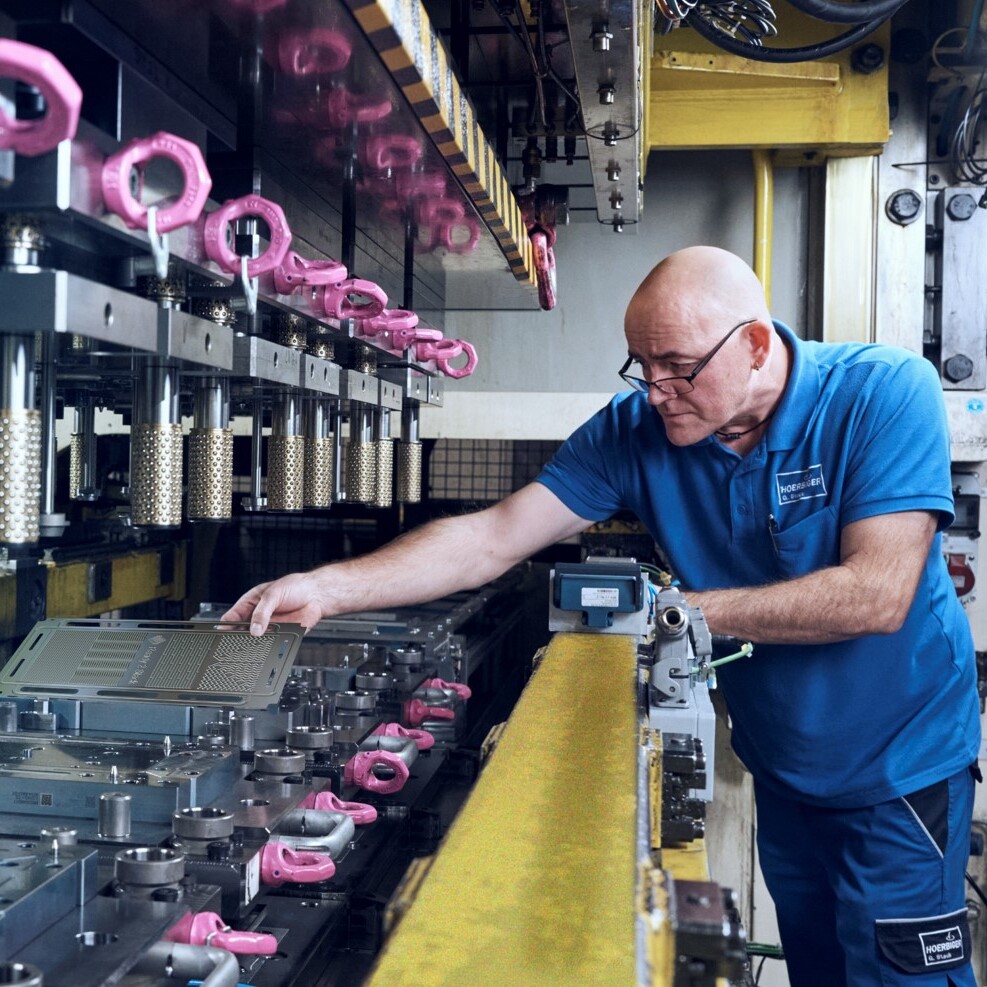
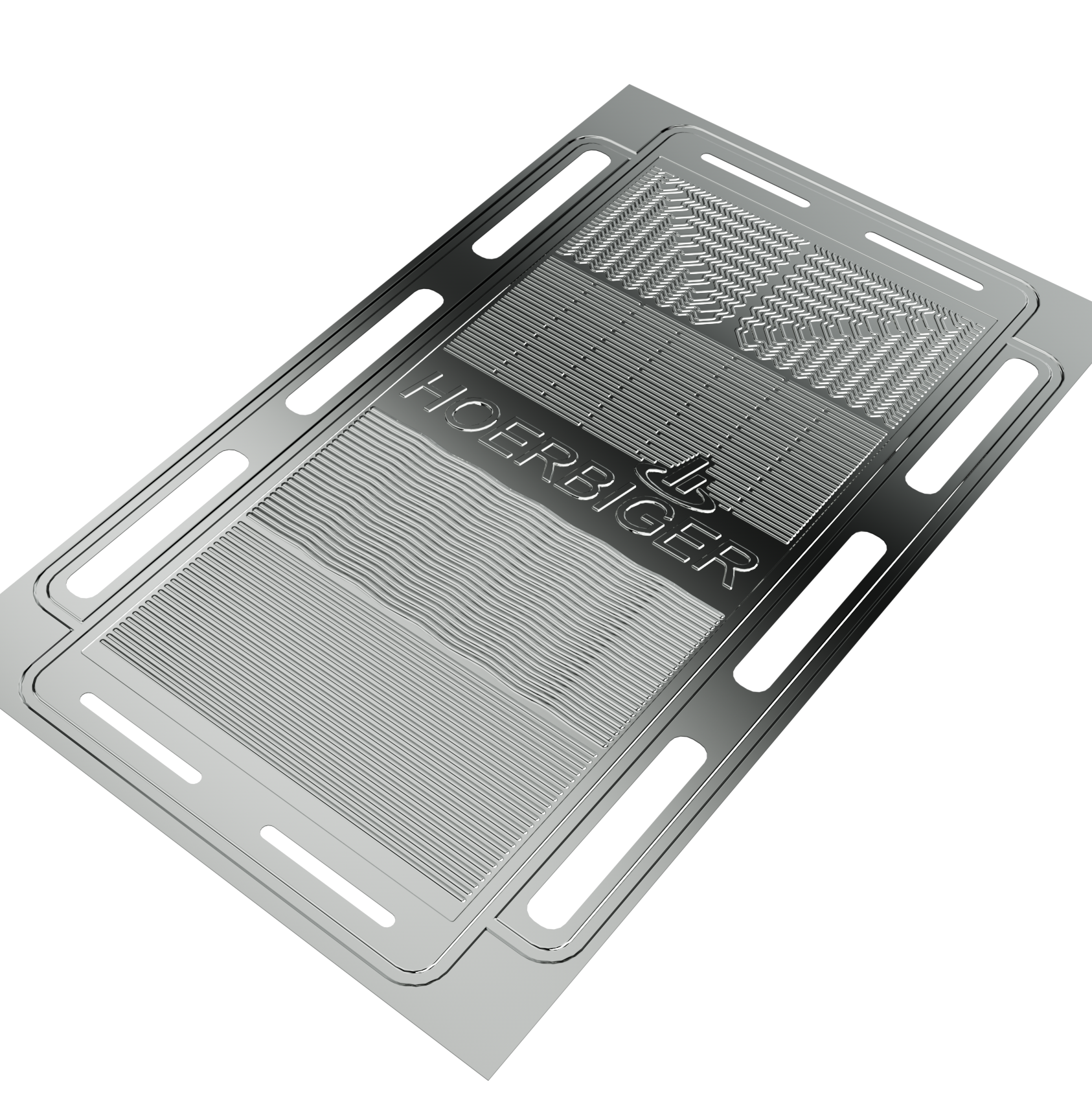
Beschichten und weitere Behandlung
Die aggressiv-oxidative Umgebung in der (PEM-)Elektrolysezelle erfordert eine robuste Oberfläche der Bipolarplatte. Hierfür bietet HOERBIGER verschiedene Lösungen basierend auf unterschiedlichen Technologien an.
Für die Hochleistungsbeschichtung der umgeformten metallischen Bipolarplatte arbeitet HOERBIGER mit einem Kooperationspartner zusammen, der langjährige Erfahrung in der Elektrochemie vorweisen kann.
Im Vordergrund steht die Erhöhung der Korrossionsbeständigkeit, sowie die Senkung des Kontaktwiderstands der Bipolarplatten. Damit werden Degradationsraten von < 4µV/h möglich, was die Lebensdauer der Stacks signifikant erhöht und die Gesamtbetriebskosten des Elektrolyseurs senkt.
Je nach Kundenanforderung sind weitere Prozessschritte nötig, darunter fällt beispielsweise das Waschen der Teile oder die Oberflächenaktivierung für den anschließenden Dichtungsauftrag. Wir entwickeln spezifische Prozesse und kümmern uns um die Industrialisierung.
Applikation der Dichtung
Die Dichtung ist nicht nur aus Sicherheitsgründen ein zentraler Bestandteil der Bipolarplatte, sondern auch für die Funktionalität von entscheidender Bedeutung. Die Dichtung ist der aggressiven Zellumgebung ausgesetzt und muss hohe Anforderungen an Temperatur- und Alterungsbeständigkeit erfüllen.
HOERBIGER bietet unterschiedliche Technologien an, dabei entscheidet die Anwendung und letztendlich die Kundenanforderung. Über Spritzguss und Dispensen aller gängigen Materialien (FKM, EPDM, Silikon) sind wir der Partner für integrierte Lösungen.
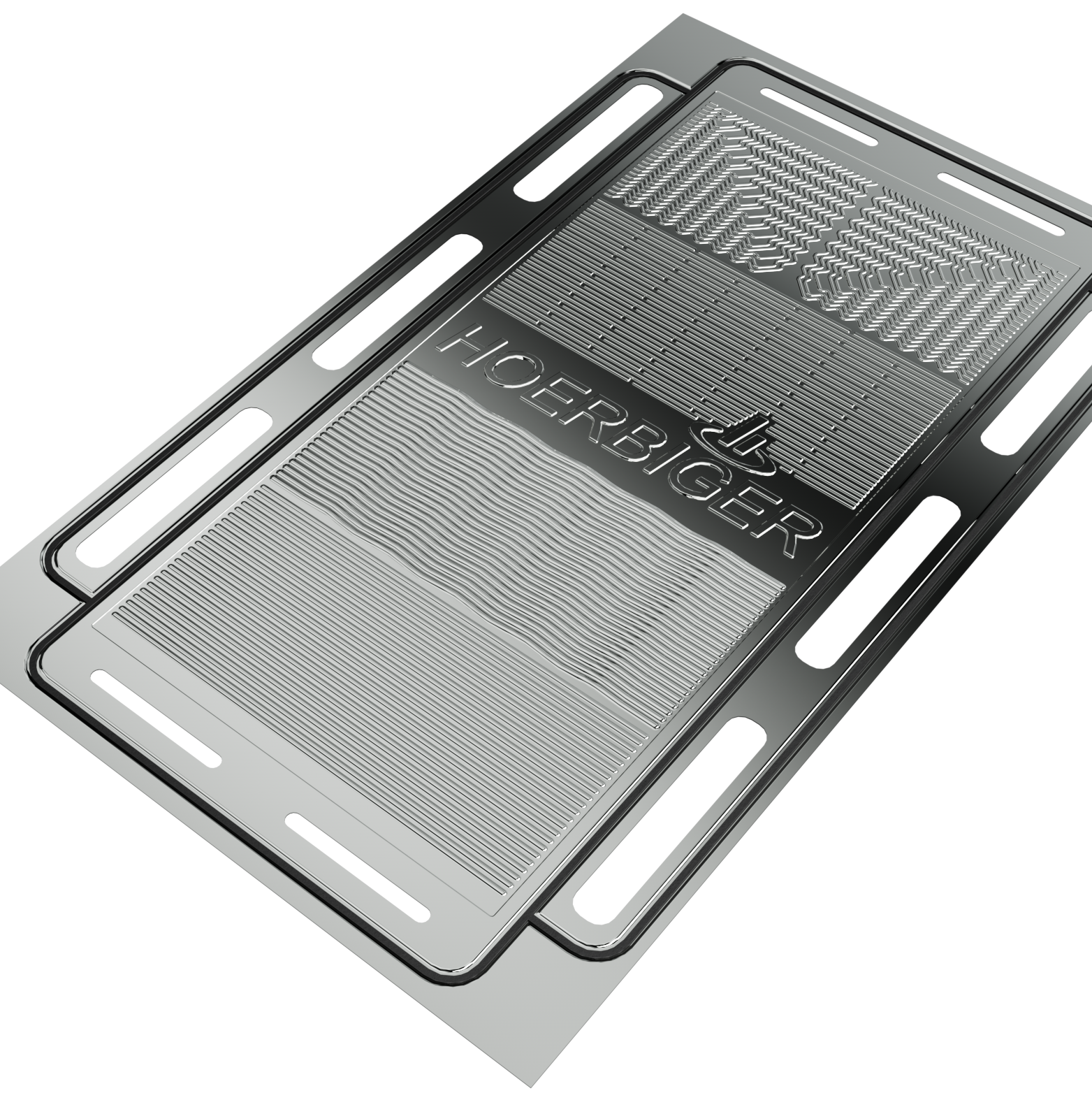
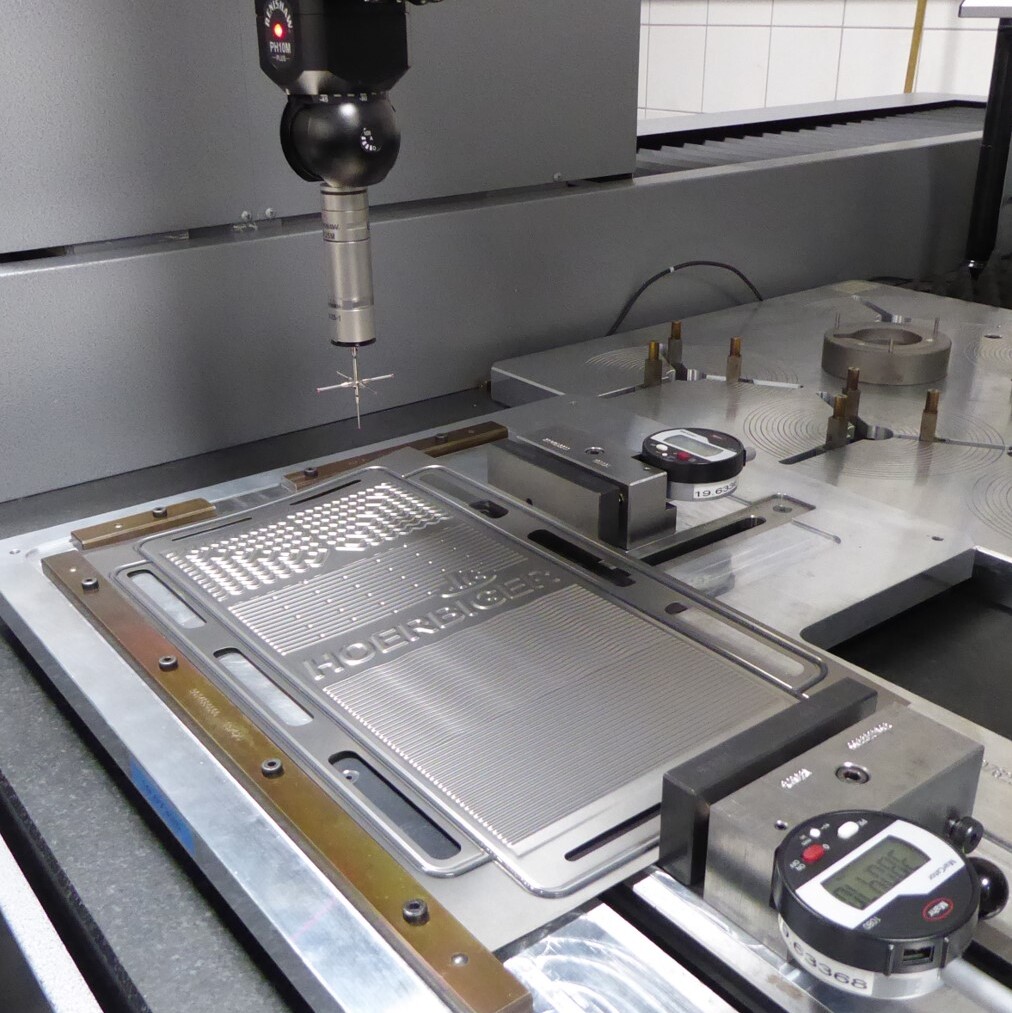
Qualitätskontrolle
Die abschließende Qualitätskontrolle stellt die Einhaltung aller leistungsbestimmenden Merkmale der Bipolarplatte sicher. Auch kundenspezifische Validierungen sind möglich, u. a. die Ermittlung der Leckagewerte oder auch des Kontaktwiderstands der Oberfläche. Damit sind unsere Kunden in der Lage, die Bauteile direkt zu stacken. Vorteile auf Kundenseite sind minimierter Ausschuss, reduzierter Logistikaufwand im Montagewerk, sowie reduzierte Prozesszeiten.
Erfahren Sie mehr auf unserer Produktwebsite Ready2StackTM.
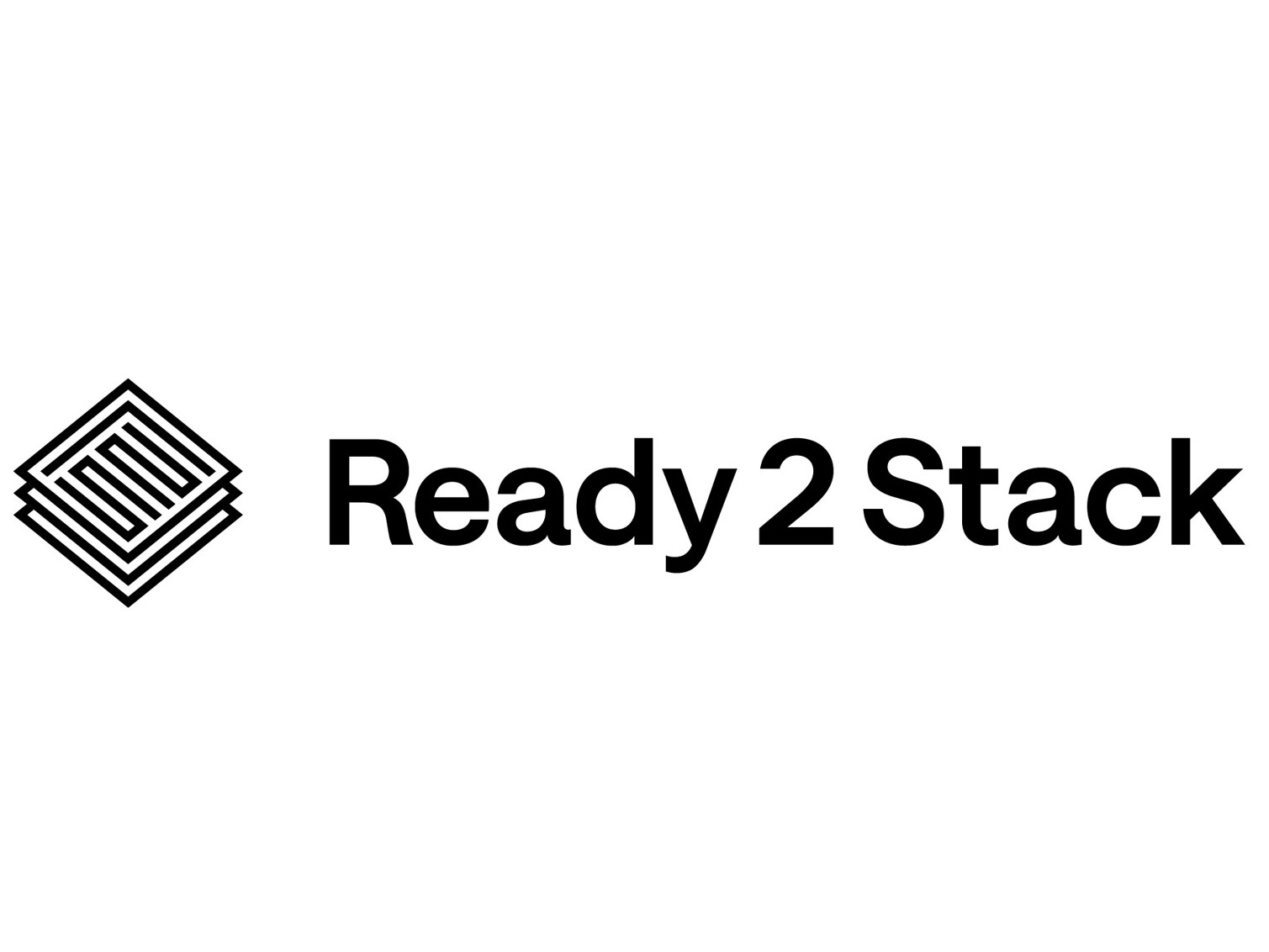
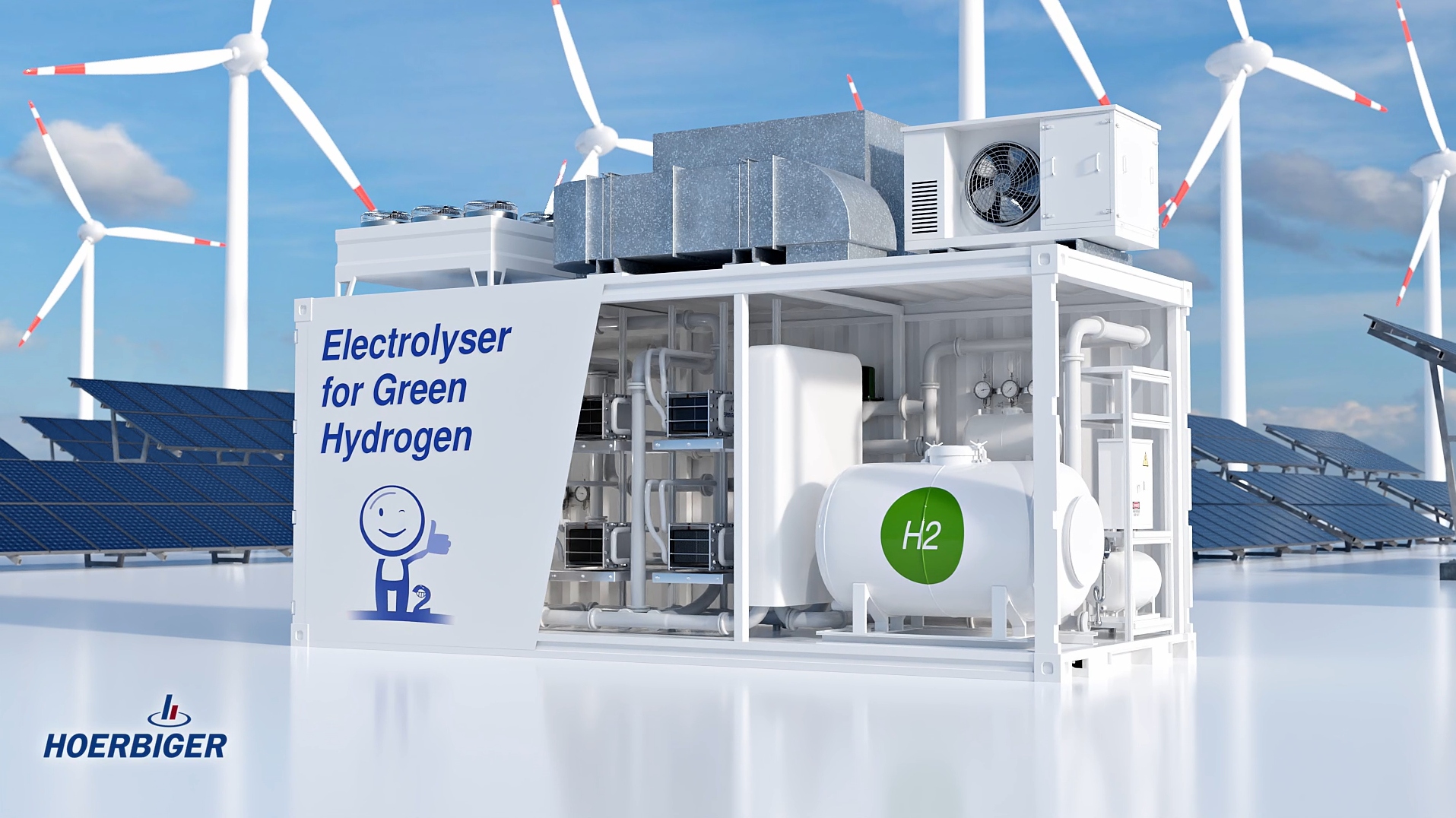
Warum Elektrolyse?
Wasserstoff gilt aufgrund seiner überragenden Speicherfähigkeit als unverzichtbares Schlüsselelement der Energiewende. Die Herstellung von Wasserstoff muss jedoch künftig ebenso wie seine Nutzung ohne CO2-Emission auskommen – andernfalls kann die Dekarbonisierung des Energie- und Wirtschaftskreislaufs kaum gelingen. Weltweit gewinnt damit die Wasserelektrolyse zunehmend an Bedeutung.
Das elektrochemische Wirkprinzip ist einfach: Wasser wird mit Strom beaufschlagt und so in dessen Bestandteile Wasserstoff und Sauerstoff zerlegt. Treibhausgase sind weder an der Reaktion beteiligt, noch werden sie für Nebenprozesse benötigt.
Trotz dieses Konzepts steht die technische Umsetzung vor anspruchsvollen Herausforderungen. Um die derzeitigen, erdölbasierten Energieträger zu ersetzten, müssen zügig enorme Mengen an Wasserstoff hergestellt werden können. Dafür wird eine große Stückzahl an Elektrolyseuren in kurzer Zeit benötigt. Letztere müssen eine optimierte Leistungsdichte, einen höchstmöglichen Wirkungsgrad sowie eine lange Lebensdauer aufweisen – nur so sind akzeptable „Total cost of ownership – TCO“ möglich.
Dies kann nur gelingen, wenn die Entwicklung und Produktion jeder Einzelkomponente optimiert und aufeinander abgestimmt wird. HOERBIGER hilft genau dieses Ziel zu erreichen. Als langjähriger Lieferant der Automobilindustrie sind wir auf die Herstellung von komplexen und eng tolerierten Metallkomponenten in hohen Stückzahlen und zu wettbewerbsfähigen Preisen spezialisiert. Unsere Fertigungs- und Engineering-Kompetenz erlaubt es uns, maßgeschneiderte Lösungen für unsere Kunden zu entwickeln und so das bestmögliche Ergebnis an Kosteneffizienz und Produktqualität zu erreichen.
Haben Sie Fragen?
Wir haben die Antworten - kontaktieren Sie uns noch heute.
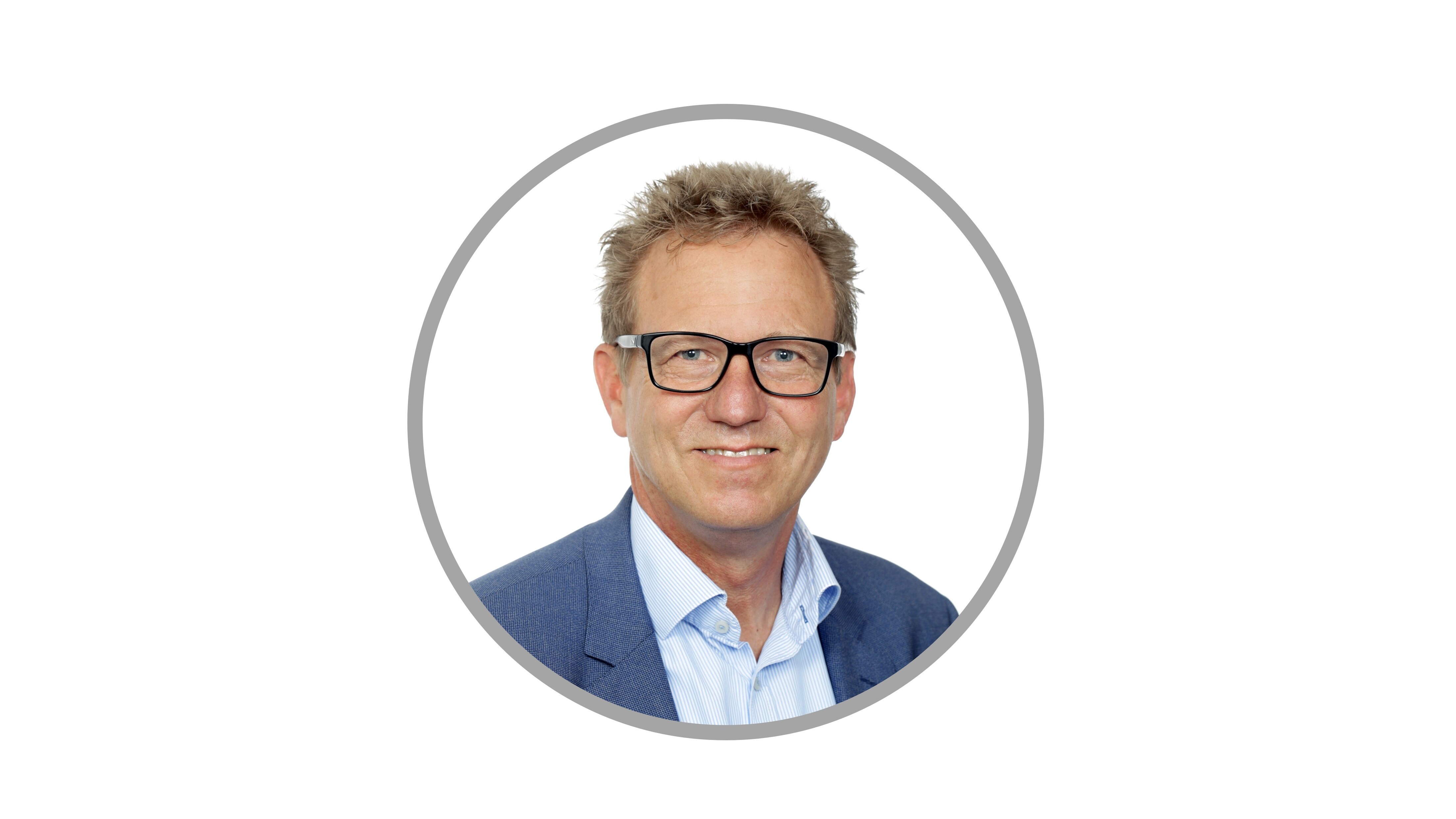
Lothar Kern
Head of Sales
+49 8861 2566 2070
electrolysercomponents@hoerbiger.com